ceramic
3D Printing
Achieving High-Quality and High-Performance
Ceramic Stereolithography Technology
Ceramic stereolithography technology combines vat photopolymerization and DLP (Digital Light Processing) technologies to selectively photopolymerize ceramic fillers and build up three-dimensional structures layer by layer.”
We offer a contract development service using ceramic 3D printers with stereolithography technology, which enables the production of high-functioning ceramics with material properties similar to conventional manufacturing methods. This technology allows for delicate and complex shapes, as well as precise customization, which are difficult to achieve with traditional molding and cutting methods.
-
Point.1
Able to create complex shapes that were previously difficult to achieve
-
Point.2
Advanced firing technology unique to a specialized ceramics company
-
Point.3
Complete in-house production of all manufacturing processes
-
Point.4
Comprehensive management and inspection system across all processes
-
Point.5
Peace of mind and short lead times due to domestic manufacturing
-
Point.6
Improvement of product functionality through complex shapes
Examples of Ceramic 3D Printing Manufacturing
For Industrial Use
By using ceramic stereolithography technology, it is possible to create products that cannot be molded or assembled by other methods
Through the exploration of new designs, we can improve product functionality and develop value-driven applications.
-
Micro-sized Heat Exchanger
-
Abrasion-Resistant Nozzle
-
Parts for the Manufacturing Process of Chemical Products
-
Corrosion-Resistant Mixer
Small Parts
We can manufacture extremely complex and precise ceramic parts, which were impossible with injection molding, within sub-millimeter dimensions, and with high accuracy and reproducibility. Since stereolithography technology does not require molds, issues related to shear force during mold filling do not occur.
For example, even with very small parts such as wall thickness or hole diameter of just 100 μm, or parts that require high surface quality, we achieve higher quality than conventional ceramic 3D printed products.
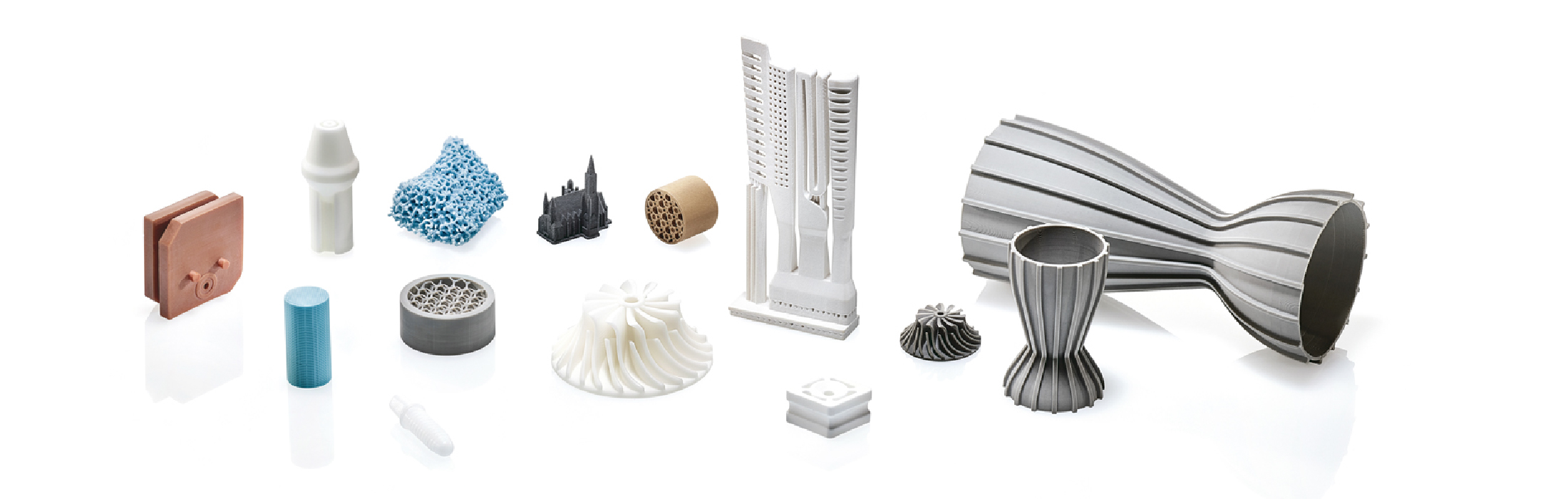
Regenerative Medicine Field
We can create regenerative medical components that fit the defect site from CAD data obtained from the patient’s body.
In addition, it can handle delicate hollow and lattice shapes and can be applied to cell scaffolds.
It is also possible to manufacture surgical tools such as screws and mini plates.
-
Tricalcium Phosphate
-
Hydroxyapatite
Materials for Regenerative Medicine
LithaBone TCP 380(Ca3Po4) | LithaBone TCP 480 | LithaBone ATZ 980 | |
---|---|---|---|
Materials | Tricalcium Phosphate | Hydroxyapatite | Toughened Alumina Zirconia |
Density | 3.07 g/cm2 (T.D.) 99.0% (R.D.) | 3.16g/cm2(T.D.)92-98%(R.D.) | 5.5g/cm2(T.D.) 99% (R.D.) |
Ceramic Powder | Compliant with ASTM standard F1088-04a(Applicable to Bioimplants) | Compliant with ASTM standard F1185(Applicable to Bioimplants) | White |
Three-Point Bending Test | 34 MPa | (120-150MPa) | 750MPa |
Color | White | Aqua Blue | |
Cytotoxicity | None(ISO 10993-5) | None(ISO 10993-5) | |
Inflammation、Dermal Reactivity | None(ISO 10993-10) | ||
Genotoxicity、Carcinogenicity、Reproductive Toxicity | None(ISO 10993-3) | ||
Maximum Wall Thickness | 20mm | ||
Coefficient of Thermal Expansion | 13.5 |
Dental Medical Field
The currently popular CAD/CAM technology for creating dental prostheses involves machining from ceramic blocks, resulting in 90% of the material becoming waste. On the other hand, the waste from stereolithography technology is about 20%, reducing the unnecessary consumption of materials.
We offer a variety of high-strength zirconia suitable for dental prosthetics such as all-ceramic crowns and dental implants. In addition, there is no significant difference in bending strength between zirconia after 3D printing and zirconia after CAD/CAM.(In-house Research)
-
Dental Implants
Regenerative Medical Materials
LithaCOn 3Y 210 | |
---|---|
Materials | Fully Stabilized Zirconia(3mol%Y₂O₃) |
Four-Point Bending Test | 930MPa |
Density | 6.088 g/cm³(T.D.)99.4%(R.D.) |
Surface Roughness | <1.0μm |
Cytotoxicity | None(ISO 10993-5) |
Inflammation、Dermal Reactivity | None(ISO 10993-5) |
Genotoxicity、Carcinogenicity、Reproductive Toxicity | None(ISO 10993-5) |
Comparison of Material Consumption Rates
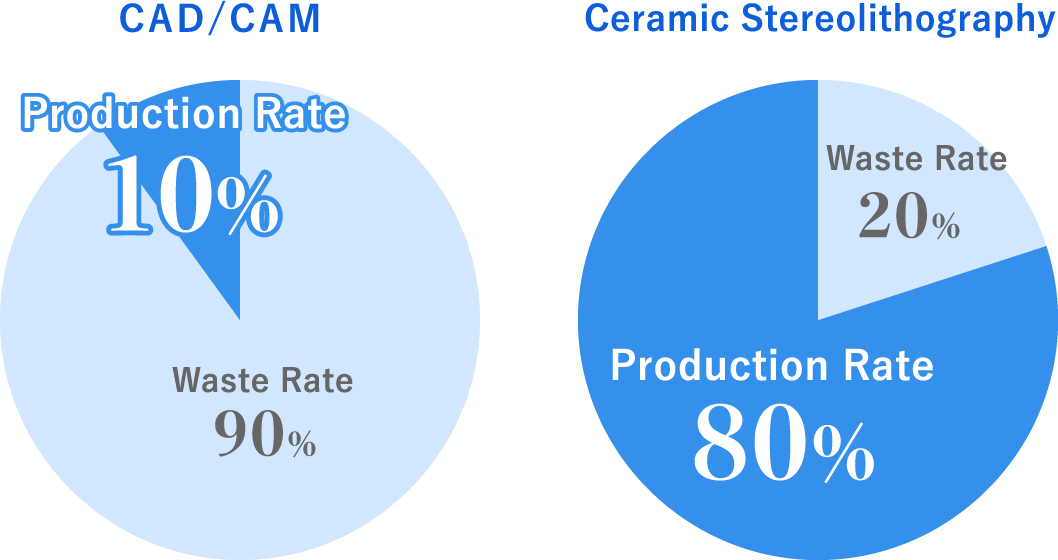
Project Workflow
-
Contact Us
-
Meeting
Meetings will be conducted as necessary.
-
Provide 3D Data (STL File)
It will take time if there is no data available.
-
Confirmation of Production Feasibility, Quotation, Delivery Time, Specifications, etc.
We will contact you after reviewing the provided data.
-
molding
We will proceed to the fabrication process based on the data.
-
Sintering・Pre-treatment・Degreasing
Depending on the complexity of the fabrication, it generally takes one of three timeframes: 7 days, 10 days, or 14 days.
-
Cleaning and Inspection
We will respond according to the purpose.
-
Delivery
We will deliver the finished product.