セラミック
3Dプリンティング
高品質・高性能を実現する
セラミック光造形技術
セラミック光造形技術とは、パット光重合技術とDLP(Degital Light Processing)技術を組み合わせて、
セラミック充填材を選択的に光重合し、三次元構造を積層造形する技術です。
従来の製造法と同様の材料特性を持つ高機能セラミックを、従来の成型・切削手法では困難な繊細で複雑な形状や、
精密なカスタマイズを可能にする、光造形技術を用いたセラミック3Dプリンターによる受託開発サービスをご提供します。
-
Point.1
従来困難だった複雑造形を作製可能
-
Point.2
セラミック専門会社ならではの高度な焼成技術
-
Point.3
全ての製造工程を自社で一貫生産
-
Point.4
全工程にわたる管理・検査体制
-
Point.5
国内製造のため安心・短納期
-
Point.6
複雑造形による製品の機能性改善
セラミック3Dプリンティング製造例
工業用
セラミック光造形技術を用いることで他の方法では成型や組み立てが不可能な製品も作製できます。
新たな設計の探索を通して製品機能を向上させ、価値駆動型の用途を開発することができます。
-
マイクロサイズの熱交換器
-
耐摩擦ノズル
-
化学製品の製造工程の部品
-
耐腐食性ミキサー
小型部品
射出成型法では不可能だった非常に複雑で精密なセラミック部品を、mm単位以下の寸法範囲で、かつ高度な正確性と再現性で作製できます。光造形技術では金型を必要としないため、金型内への流入に伴う剪断力(せんだんりょく)の問題も起きません。
例えば壁厚や穴径がわずか100μmといった非常に小さな部品や、高井表面品質が求められる部品でも、従来のセラミック3Dプリンター製造品を超える高度な品質を実現します。
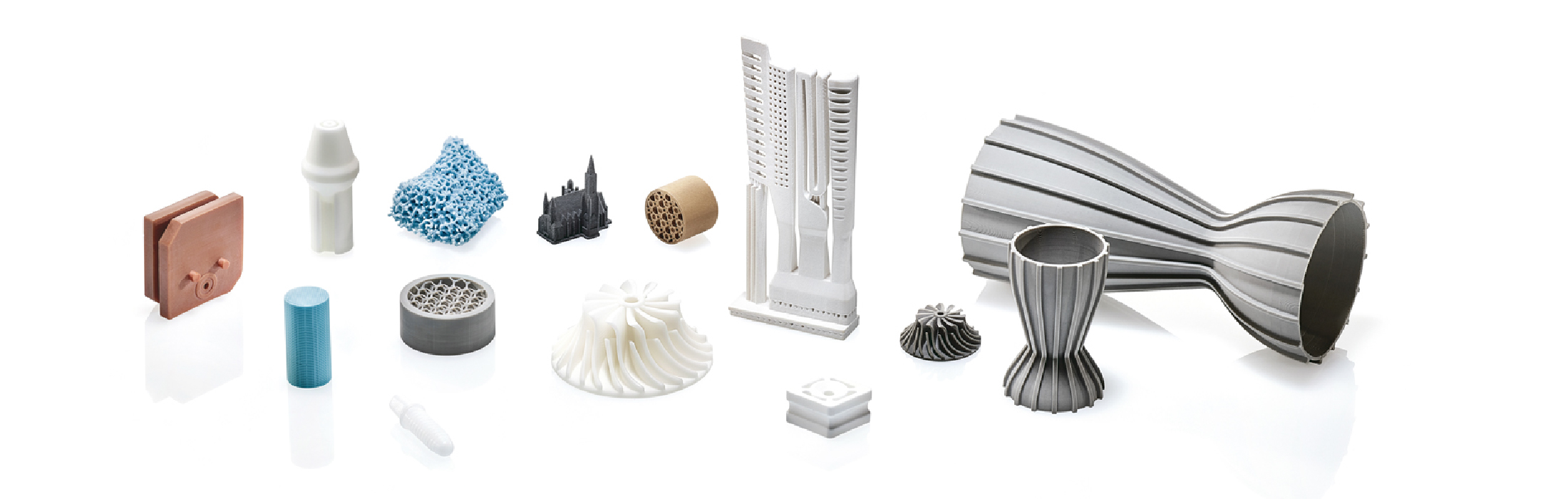
再生医療分野
患者様の生体から得られたCADデータから、欠損部位に適合する再生医療用部品を作製できます。
また、空洞や格子状の繊細な形状にも対応し、細胞のスキャフォールドに応用可能。
スクリューやミニプレートなどの外科処置用治具も作製可能です。
-
リン酸三カルシウム(TCP)
-
ハイドロキシアパタイト (HA)
再生医療用材料
LithaBone TCP 380(Ca3Po4) | LithaBone TCP 480 | LithaBone ATZ 980 | |
---|---|---|---|
材料 | リン酸三カルシウム(β-TCP) | ハイドロキシアパタイト | 強化アルミナジルコニア |
密度 | 3.07 g/cm2 (T.D.) 99.0% (R.D.) | 3.16g/cm2(T.D.)92-98%(R.D.) | 5.5g/cm2(T.D.) 99% (R.D.) |
セラミック粉末 | ASTM standard F1088-04aに準拠 (生体インプラントに適用可能) |
ASTM standard F1185に準拠 (生体インプラントに適用可能) |
白 |
3点曲げ試験 | 34 MPa | (120-150MPa) | 750MPa |
色 | 白 | アクアブルー | |
細胞毒性 | なし(ISO 10993-5) | なし(ISO 10993-5) | |
炎症、皮膚感作性 | なし(ISO 10993-10) | ||
遺伝毒性、発がん性、生殖毒性 | なし(ISO 10993-3) | ||
最大肉厚 | 20mm | ||
熱膨張係数(ppm/K) | 13.5 |
歯科医療分野
現在歯科補綴物の作製でポピュラーなCAD/CAM技術はセラミックブロックから切削するため、材料の9割は廃棄物となります。一方、光造形技術の廃棄物は2割程度となり、材料の無駄な消費を抑えます。
オールセラミッククラウンや歯科用インプラントなどの歯科補綴物に適した高強度のジルコニアを複数ご用意しております。なお、3Dプリンティング後とCAD/CAM後のジルコニアの曲げ強度比較において、両者に大きな差はありません。(自社調べ)
-
歯科用インプラント
再生医療用材料
LithaCOn 3Y 210 | |
---|---|
材料 | 安定化ジルコニア(3mol%Y₂O₃) |
4点曲げ試験 | 930MPa |
密度 | 6.088 g/cm³(T.D.)99.4%(R.D.) |
表面粗さ(Ra) | <1.0μm |
細胞毒性 | なし(ISO 10993-5) |
炎症、皮膚感作性 | なし(ISO 10993-10) |
遺伝毒性、発がん性、生殖毒性 | なし(ISO 10993-3) |
材料の消費量の比較
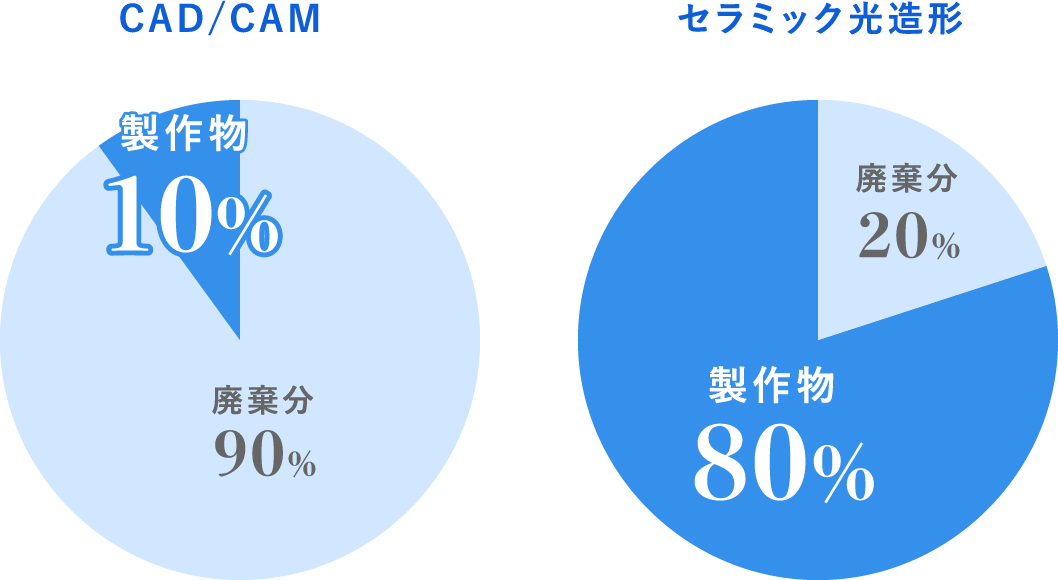
プロジェクトの進め方
-
お問い合わせ
-
お打ち合わせ
必要に応じて
お打ち合わせを行います。 -
3Dデータ(stlファイル)
ご提供データがない場合は
時間がかかります。 -
製作可否の確認、見積、納期、仕様などのご連絡
提供いただいたデータを
確認後、ご連絡します。 -
造形
データを元に
造形工程に入ります。 -
焼成・前処理・脱脂
造形の難度によって大まかに
3パターンの時間を要します。
(7日/10日/14日) -
洗浄・検査
用途に応じて対応します。
-
納品
完成した品物をお届けします。